David
Griffiths has been with us for an intensive three day
work-in. He and his wife Pennie will soon fly back to
Australia from their London base in early March after their
6 month UK visit. David is taking a last chance to turn a
spanner before he goes back home. He brought with him some
much needed CX spares which were dispatched by surface mail
from Sydney by his son Gwilym in November and which arrived
at Wood Green just before David travelled north. The Aussies
really do have the just-in-time concept down to a fine art!
David takes up the story and the captions below are his as
well:
Saturday, Sunday and Monday were to be serious work days -
clutch parts from Turramurra Stores came into play - the
clutch release and clutch brake mechanism was rebuilt,
assembled to the gearbox and the whole mated to the engine.
It took four of us - Paul, Davie, John and me to lift the
gearbox onto a trolley jack. Albion used to build things
solidly.
Some uncertainty now entered the proceedings. Brought from
my collection in Sydney last September had been a newly
relined clutch disc with 1/4" thick linings on the
assumption that a sixty year old bus would have had its
flywheel facing and its clutch pressure plate resurfaced
several times, necessitating an oversize clutch disc.
Instead the flywheel facing and pressure plate were found to
be unusable, full of heat stress cracks, so replacements had
been found in Scotland, amongst Davie's truck parts. Would
there be room for these full-thickness parts and an over
thick clutch disc in the range of adjustment available? Only
one way to find out, although some rough measurements were
taken to establish that it was not out of the question.
With engine and gearbox re-united and everything adjusted to
suit, there was a millimetre or so of internal clearance of
clutch finger pivot studs from the external clutch housing.
Final adjustment must await the refitting of the engine to
the bus and connecting up of the clutch pedal.
|
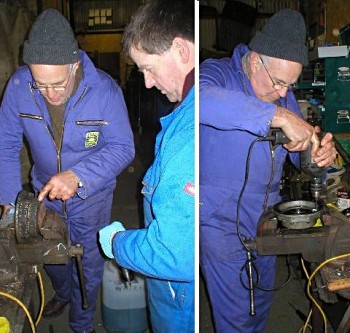 |
Left: An Albion CX19
owner from Australia, in Scotland to learn some
maintenance tricks, examines the original CX clutch throwout
bearing
while Davie Philp looks on. It was seized so a replacement
from an HD,
somewhat the worse for wear, was sourced. David points to a
rusted in
lockscrew and the discussion is about how to release it. It
was eventually drilled
out, the hole retapped and a new screw made from a suitable
bolt.
Right: DG drills out the rivets from the friction
lining on the clutch throwout
bearing chosen as a replacement. |
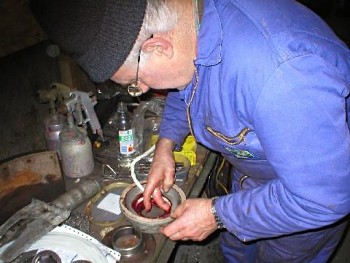 |
The ball
race in the replacement clutch throwout bearing has just
been
repacked with red high melting point grease of a very modern
formula (as used
in Volvo buses). A new felt seal is pressed into place by
the Australian
apprentice. |
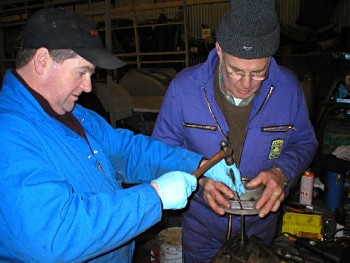 |
DP and DG
set rivets to secure the new friction lining, newly sourced
from
Australia, to the clutch throwout housing. |
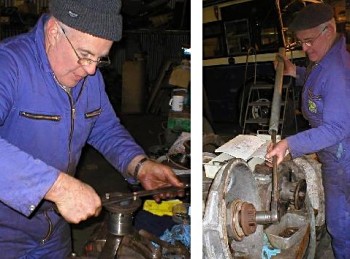 |
Left: The thrust ring
at the rear of the clutch throwout housing gets its thread
freed up by moving it to and fro on the withdrawal sleeve.
By great good
fortune, a hand made tool for some other purpose, found in
the workshop,
makes a perfect bracket to mount in the vice for holding the
sleeve from
rotating. Right: After a great deal of checking that
all was in order, DG refits the clutch throwout housing and
clutch brake disk, visible to the left of the socket wrench. |
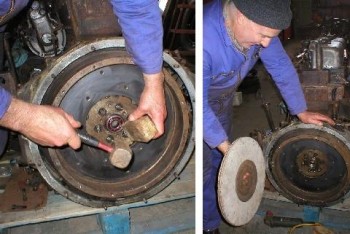 |
Left:
Thoroughly cleaned up and packed with HMP grease, the clutch
spigot race is refitted into the flywheel. Surrounding it is
the "new" flywheel facing from Davie's stock of HD parts.
Right: Carried from Australia in Rick Robinson's
baggage, the clutch disc, newly refaced in the NSW Department
of Government Transport workshops several decades ago, is
about to be placed against the flywheel facing, prior to
refitting the clutch pressure plate and its housing. |
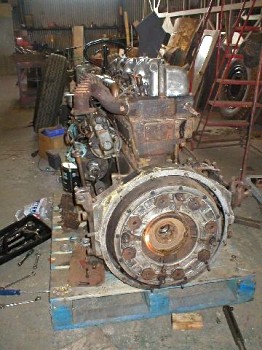 |
The clutch
housing and its pressure plate secured to the flywheel. The
engine valve rocker gear covers have been thoroughly cleaned
and will be sent away for polishing. The engine will be
steam cleaned again and painted. |
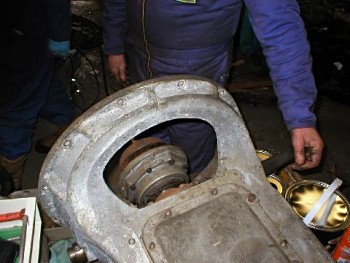 |
Checking the
action of the clutch release lever and throwout housing. as
the
housing moves forward it releases the clutch and then comes
against the
clutch brake disc, visible in the photo in front of the
aluminium octagonal housing.
Synchronising these two actions is critical to ensure
comfortable upward
gear changes. |
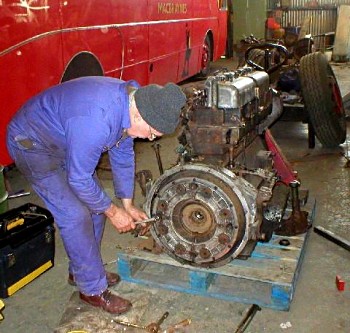 |
Tightening
the clutch housing securing screws after ensuring that the
clutch
disc is perfectly centred between pressure plate and
flywheel. |
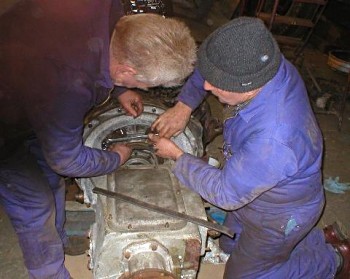 |
John and
David adjust the clutch release fingers. On the assumption
that the
pressure plate and flywheel facing would have had several
resurfacing in their
lives, the relined clutch disc from Oz was supplied with
1/4" linings instead of
standard 3/16". Therefore there existed some doubt, after
using an almost
new pressure plate and flywheel facing, that the disc would
fit into the range of adjustment available - all seems well
however. The clutch release pivot studs
just clear the inside of the gearbox bell housing by a
millimetre or two. |
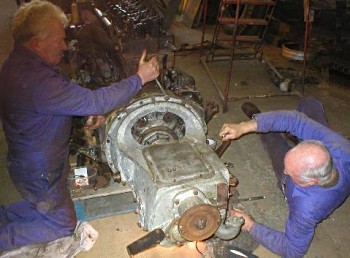 |
The rebuilt
gearbox has been successfully mated to the engine. John and
David
fit new securing nuts all around the bell housing. With the
newly overhauled water pump fitted the engine and gearbox
are ready for a final clean up and refitting
to the chassis. |
|
We would like to thank David very much for all his help and
for the donation of important spares from his CX19 stock
back home. David has shown that he is
not only capable of taking old buses to bits, but that he is
even more capable of putting them back together again!
But anyone who has seen his two projects
in Turramurra will know that anyway. David, you are
welcome back here
anytime!
|